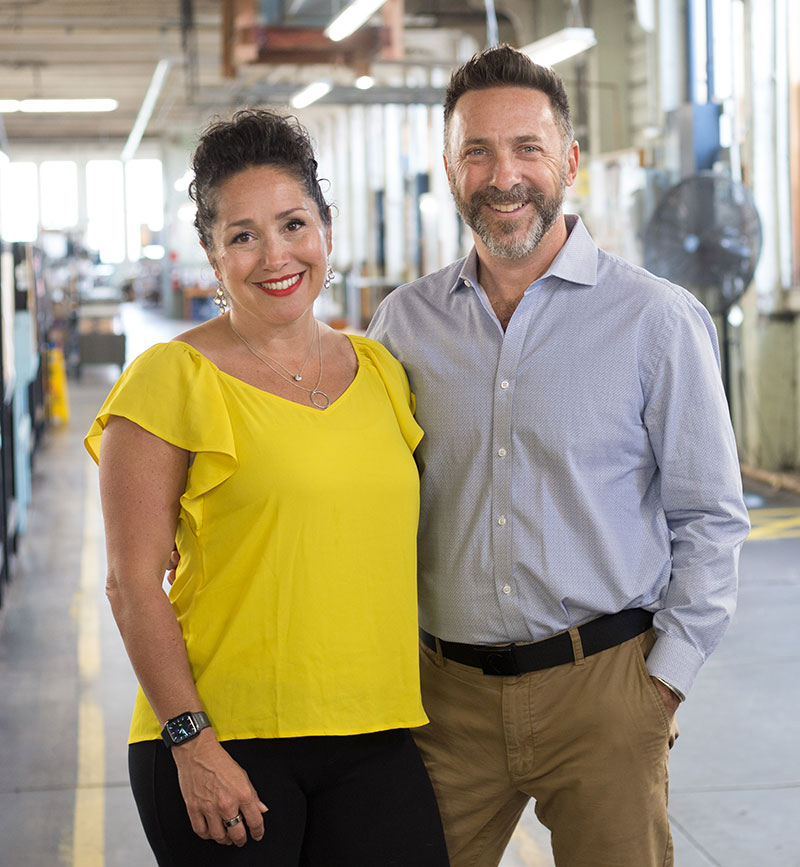
Adria & Aaron Bagshaw
VP and President at W.H. Bagshaw Company
W.H. Bagshaw is like a 152-year-old start-up. After being one of America's leading textile pin manufacturers, the company pivoted to Swiss machining to tap into new markets.
Swiss Pivot: Company Moves from Textile Pins to Precision CNC Parts
America's first factory was a textile mill built in 1790 for the mechanized carding and spinning of cotton. Hydro-powered textile mills soon sprang up along New England waterways, and so did the machining industries that supported them. Among those companies is W.H. Bagshaw Company.
Founded in 1870 in the historical textile town of Lowell, Massachusetts, W.H. Bagshaw moved a few miles up the Merrimack River to Nashua, New Hampshire, in 1949, where it continued as one of America's largest producers of textile and specialty pins. Pins start with a small diameter coiled wire which W.H. Bagshaw cuts to length, grinds to a taper, deburrs, adds a custom point or ball radius, heat treats, and polishes.
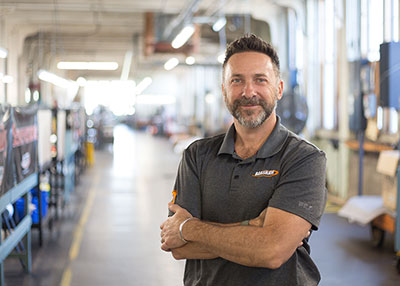
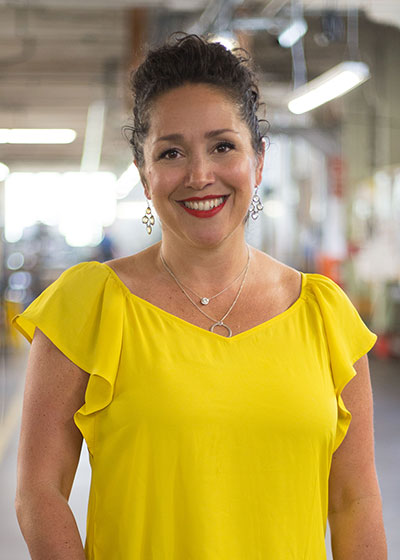
In the early 2000s, Aaron Bagshaw, company president and fifth generation owner, recognized that the company was too heavily weighted in textiles. Adria Bagshaw, W.H. Bagshaw vice president, also saw the writing on the wall.
I knew the company was at a big, big crossroads,
says Adria, who came from a career with a much larger electronics manufacturing company and with a degree in business and economics. Textiles and hand tools were probably a quarter of our business at the time, and they were rapidly moving to Mexico and China.
Creating a New Identity
Aaron notes that, We have been in continuous operation since 1870, so we do a lot of things right. At the same time, we were missing out on applications in the medical, aerospace, automotive, and other industries. Engineers would send us prints for pin-shaped parts to quote on them, but we didn't have the equipment. I realized that adding Swiss-style CNC machines would allow us to tap these markets and diversify our business.
The quest to diversify and modernize led Aaron and Adria to IMTS 2004 to explore Swiss CNCs and other precision CNC turning and machining centers.
Going to IMTS really opened our eyes to those new manufacturing opportunities and enabled us to create a new identity,” says Aaron.
Today the company operates a fleet of 34 Swiss CNC machines such as the Citizen Cincom L12. With 15,000 RPM main spindle speeds, the L12 can have a maximum of 28 mounted tools, with 4 live spindles included as standard. Live spindles mounted on the gang tool slide can be easily removed and mounted on the backside for work on the sub-spindle if the application demands. At IMTS, the Aaron and Adria plan to see the new Miyano BNE-65MYY lathe (Miyano is wholly-owned by Citizen). This machine will be on display for the first time at IMTS. It features a new operator interface, a larger viewing window, 65 mm (2.56 in.) bar capacity and a Y axis equipped to serve both upper and lower turrets; there are also models equipped with a B axis on the upper turret.
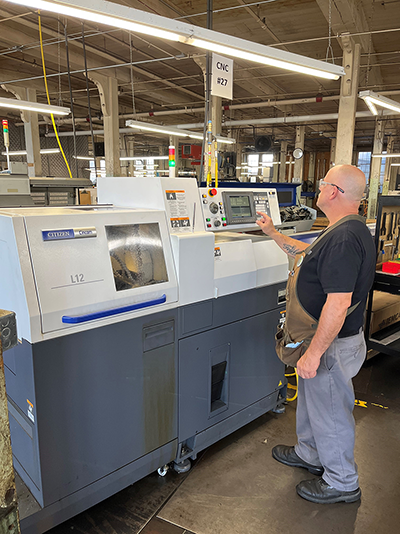
Expanding into precision small-part machining allows us to make the components that go into the thing that makes the bigger things go, from medical equipment to cars to aerospace to appliances. Everything we manufacture goes into something else, so we put quality into every manufacturing step,
says Aaron.
We also discovered cleaning systems and our ERP provider, ECI Software Solutions – better known as jobBOSS2 – at IMTS 2004,
says Adria.
IMTS Playbook
In addition to Aaron and Adria, W.H. Bagshaw typically sends a handful of others to IMTS. The specific individuals vary, but one employee always attends.
Lou Davis is our CNC manager and very first CNC employee. He just celebrated 16 years with us. He loves IMTS – it's like Christmas for him,” says Adria.
To make effective use of time at the show, W.H. Bagshaw constructs a literal playbook for each attendee.
It's a three-ring binder that outlines our objectives, and it's tied to a one-page strategic plan,
says Aaron. Depending on who's going, I try to allocate resources accordingly. Each person has a playbook, and we divide and conquer. We reconvene at lunch to check progress, then gather again for dinner.
At IMTS, Aaron and Adria will be looking for CAD/CAM software, chip management solutions, and any options for updating their pin manufacturing process.
Adria says, “Everything we have today is the result of going to IMTS, walking through those doors, and seeing all the amazing technology. It's a great atmosphere. It's like walking into a living room that's set up as a CNC shop with people smiling and ready to help you.”