Angelo Biondo & Joshua Ponzetti
Vice President & Director of Operations CAM Logic, Inc.
Bringing Solutions Up the Supply Chain
Putting all your chips on the table is a risky proposition, but the leadership team at CAM Logic, Inc. went all in with a solution-based proposition to differentiate itself from its competitors. CAM Logic's solution based offering consists of Siemens PLM Software, Markforged 3D printing hardware, engineering and design, quality control, and manufacturing.
We had a wonderful legacy customer base from our software business and were already a trusted advisor in their eyes,
says Vice-president Angelo Biondo. We just needed to prove our new vision.
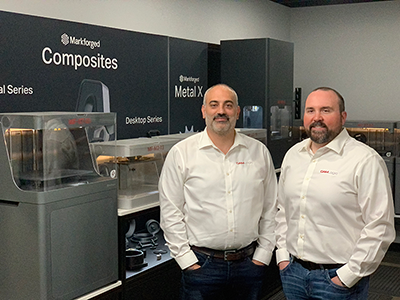
Based in Auburn Hills, Mich., CAM Logic targets other small- and medium-sized businesses (SMBs), primarily Tier 1, 2 and 3 automotive suppliers and SMB OEMs in the metro-Detroit area. The company was founded as a value-added reseller of software for CAD, CAM, CAE, PDM, and PLM. CAM Logic offered a degree of engineering services, but Biondo knew the company needed more of a competitive edge.
Prior to joining CAM Logic, Biondo was CAM Logic's banker, which provided him insight in the business model and financial make-up. Biondo's vision to differentiate CAM Logic was in full development when Yvonne Wiedemann, former Account Manager, decided to purchase the company. Having ownership now in full support of his vision, Biondo & Wiedemann's next key move was to lure back Joshua Ponzetti. An applications engineer who had worked for CAM Logic 10 years prior, Ponzetti now had two decades of experience and would be perfect as the company's Director of Operations.
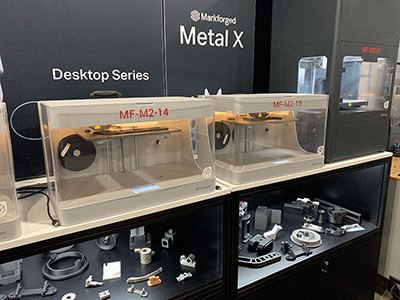
With ‘Ponz’ on board, it set the stage for our ability to become a complete solution provider,
says Biondo. We are not just a VAR for Siemens software and Markforged printers – we use these products to deliver design and engineering services and offer 3D printing and fabrication services, respectively,
says Biondo.
For the last five years, CAM Logic has focused on helping Detroit-area OEMs and SMBs understand the role of additive manufacturing in the automotive supply chain. The industry is very structured, so it takes attention to detail whenever suppliers suggest change.
Where we've found the most meaningful existence for AM has been for light-weighting the assembly side of the automotive industry,
says Ponzetti. We don't make parts for cars, we make the parts that move cars down the assembly line. Through DFAM and lightweight composites, we show customers how they can extract costs when moving parts from Point A to Point B.
Redesigning an Accumulator Pallet
A recent project for a well-known OEM encapsulates CAM Logic's end to end abilities. The initial design called for a steel weldment, on an accumulator pallet for the side of a vehicle, which was weight prohibitive. The second attempt was to manufacture the pallet leveraging an aluminum weldment. This, too, was over capacity. Due to CAM Logic's material properties expertise as it relates to light-weighting, CLI began to pursue a composite material solution, which resulted in a 12kg weight reduction. This achievement resulted in buy-off from the OEM and T1 company. To this day, the company's solution is ushering the body-in-white (BIW) side of a vehicle through an assembly plant.
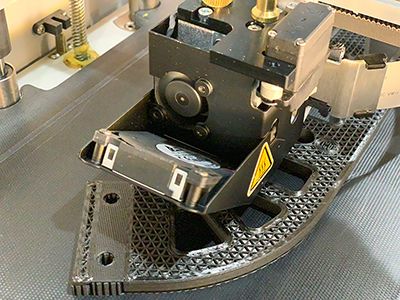
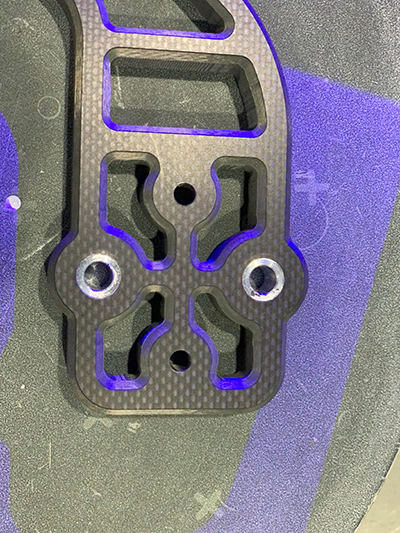
When asked about the performance of the hanger, which is a critical part of the complete pallet, Ponzetti explained, The Onyx hanger offered the best strength-to-weight ratio for the initial conveyor application. However, when we went to design a hanger for another similar conveyor system with a higher-duty requirement, we needed greater strength.
Once again, CAM Logic came through with a solution. The new design utilized a more robust, proprietary CAM Logic material yielding a higher performance. The final hanger solution was heavier, (still significantly lighter than the original customer proposed pallet), and the proprietary material provided the strength necessary to withstand the added weight and survive possible programming issues that could result in accidental collision on the assembly line.
CAM Logic believes in diversifying. We use both additive and subtractive manufacturing to create the best solution, not just the solution we can make,
says Ponzetti.
It's Like Disney World
While Markforged has some of the most reliable hardware on the market, its printers primarily use nylon-based materials. CAM Logic wanted to expand its material offerings for its manufacturing line of business – and IMTS 2018 was the place to go.
From the moment you arrive, you're overwhelmed with all of the things you are exposed to,
says Ponzetti.
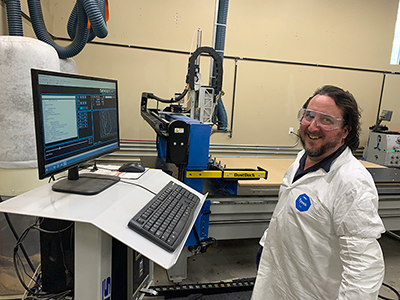
IMTS is the Disney World of manufacturing,” adds Biondo. “The breadth of different products and technologies, not to mention the industry giants all in one spot, is fantastic.”
The pair visited the Additive Manufacturing Sector and met with companies that provided printing systems for various materials, such as thermos plastics and composites. One of which was, polyethylene, because of its stability in different environments.
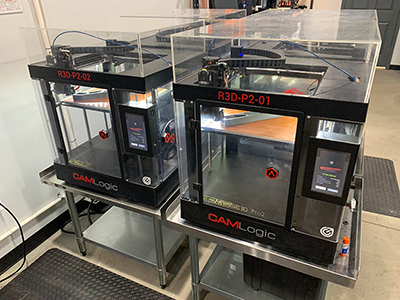
The solution we found at IMTS was the Raise3D fused filament fabrication platform,
says Ponzetti. The Raise3D platform can print with a host of different materials including general production use, and specialty filaments for electrostatic discharge resistance and flame retardance.
At IMTS, we will meet with long-running partners Siemens and Markforged, we'll continue to explore the additive offerings, and we'll meet with a lot of prospective customers,
says Biondo.
CAM Logic continues to pursue technologies and solutions that best fit the needs of their customer and their business model.
Six, 12, 18 months down the road, believe me, Ponz will come back with a Christmas list of solutions he saw at IMTS,
says Biondo.
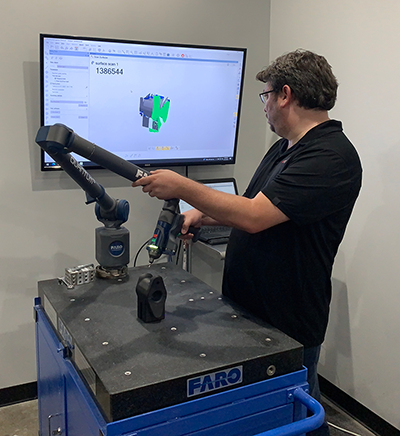
In 20 years in this industry, it has never been a question of whether or not we were going to IMTS, it was ‘Who is going this year?’” says Ponzetti. “Attending IMTS is always a top priority.”