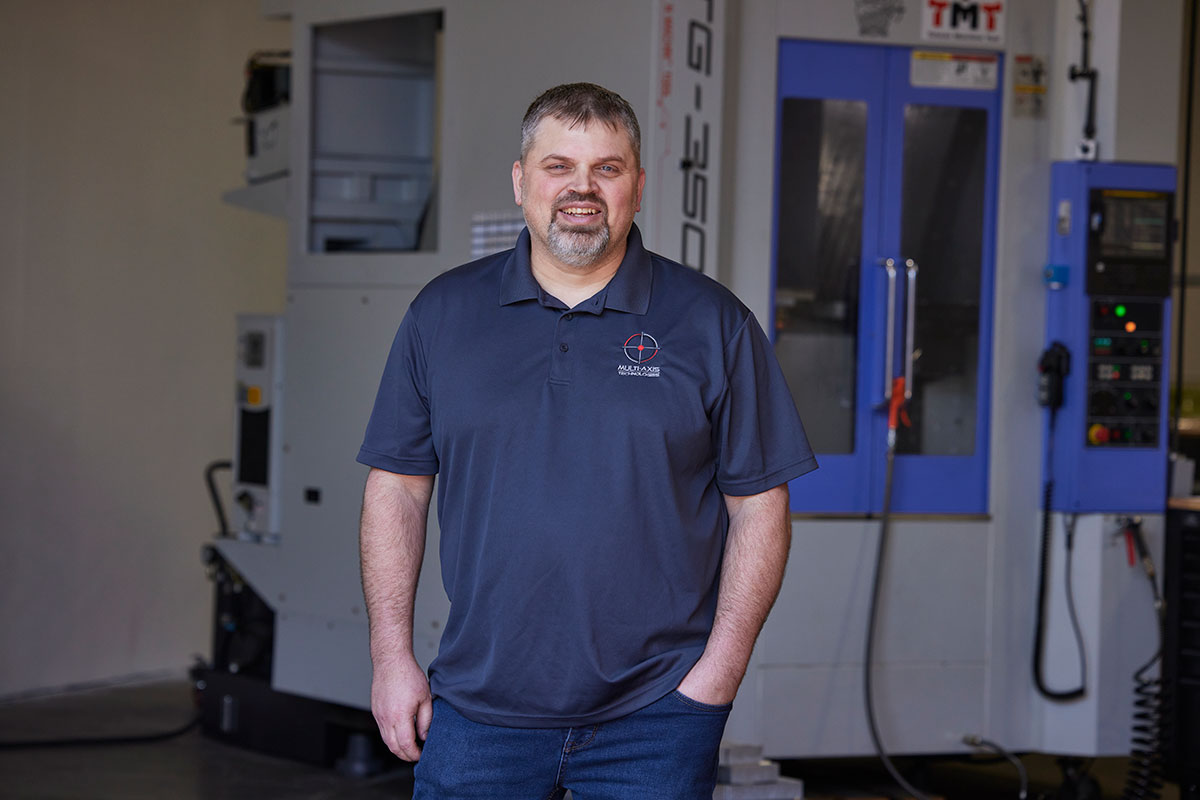
Jay Simpson
Co-Owner, Multi-Axis Technologies
Opening the Door to Opportunity
A career path in manufacturing has many doors, and Jay Simpson has opened every door. Now as co-owner of Multi-Axis Technologies, he has taken his combined 30 years of experience and put it to work for himself and his business partner.
Manufacturing knocked early on Jay Simpson's door. As a youngster, he was always intrigued with how things worked. Now, with 30 years of manufacturing experience and becoming co-owner of Multi-Axis Technologies in Kent, Wash., Simpson appreciates all the doors that have opened as a result of his inquiring mind.
“I was always taking apart the car to try to figure out what happened, taking off spark plug wires and having dad yell at me a little bit because I did it wrong,” says Simpson. “When I got introduced to the machining side, it was an awakening.”
Simpson's high school had a program called Tech Prep that was sponsored by Boeing's Seattle-area production and assembly facility. Starting in the 10th grade, Simpson earned a paid summer internship.
“Learning manufacturing fundamentals fostered a hunger for more growth,” he recalls. “I met a ton of people at Boeing that saw my potential, and they offered me an opportunity to work at Boeing.”
Simpson worked at Boeing as journeyman machinist. After four years, he had worked his way up to what Boeing calls a “grade 11 layout individual,” which was the highest hourly payscale for an hourly employee at Boeing.
“I moved on to Aerojet Rocketdyne and then from machinist into inspection, which was a paradigm shift for me,” says Simpson. “I went from making the part to now telling somebody how accurate their part was. Becoming an inspector opened a plethora of doors. I had to learn the whole GD&T (Geometric Dimensioning and Tolerancing) side of the business, how to read a drawing, and then work with machinists to show them what they needed to do to make the part right.”
Success at Aerojet Rocketdyne afforded Simpson additional opportunities, such as becoming a CAD-CAM programmer and working with manufacturing engineers to develop process improvements.
“Mastering new skills led to this gateway of door after door after door, and I just kept opening every door,” says Simpson.
Running toward the Fire
After a combined 12 years of machining and manufacturing experience at two established aerospace giants, Simpson joined Blue Origin (just “Blue” to those who worked there) in 2007. Started seven years prior by Amazon's Jeff Bezos, Blue Origin builds reusable rocket engines, launch vehicles, in-space systems, and lunar landers. The company was founded with a vision of millions of people working in space for the benefit of the earth.
“The early days of Blue, it was a methodical, controlled chaos environment, and I say that in a good way,” recalls Simpson. “We had a lot of ambition. We had a very focused founder. We had an amazing, very small team that was driven to meet a goal.”
Even with an elite collection of smart people, things go wrong and anomalies occur. At Blue, this was considered an opportunity to learn and improve; slow is smooth and smooth is fast.
“We fail early, we test often, and we learn faster. That mentality is contagious,” says Simpson. “It's like this perpetual wheel. When something goes awry, everyone wants to help. And when you want to help, you go running to the problem. You're not running away from it. You're running at the problem, and you know that you have 10 other people on each side running with you as well.”
Simpson started at Blue as an integration engineer, which was “a fancy title for doing whatever they needed me to do.” He ran through the ranks of machinist to lead machinist to supervisor to manager.
“At the end of my 14-year tenure, I ended up as the director of manufacturing for machining, welding, and programming,” says Simpson. “Daisy Kelly, who is now co-owner with me at Multi-Axis Technologies, built a team that started with four machinists. When we left, it was more than a hundred in our group alone.”
What's the Worst that Could Happen?
Where Simpson's passion always focused on technology, Daisy's passion focused on people, which led to her a career in manufacturing (see story) and positions at Blue as a buyer, planner, scheduler, and senior manufacturing manager.
Simpson recalls that, periodically, some engineers at Blue would tell them that they should start their shop, but they didn't take it to heart. Even after frustrating days where one of them would say they were done, the other would help them work through the challenge.
“Finally, one day just over coffee, we were both at even keel,” recalls Simpson. “We said, ‘I think it's time. Let's not talk about it, and let's do something about it.' We figured what's the worst that could happen? We'd just have to go back to work, so why not try? Every shot not taken is an opportunity missed.”
Quick-Turn Technology
Multi-Axis Technologies opened its doors in July of 2021 with a goal of providing very quick-turn around parts and rapid prototypes for complex solutions (see story on Jay and Daisy). Services include CNC machining, design for manufacturing, and CNC programming using Mastercam (booth# 133222).
Given Jay and Daisy's experience, the customer base skews heavily toward aerospace. The shop's proximity to Blue Origin (one mile away), Boeing, SEA-TAC airport, and 1,300 other aerospace companies in Washington State provides a wide list of local prospects, plus they connect with companies from around the country.
The strategy for outfitting the shop with peripheral equipment includes some amusing tales (see story) and the smart decision to work with Japan Machine Tools (booth #338980).
“Japan Machine Tools provided us with the opportunity to visit the factories for the machine manufactures to help with the selection process,” says Simpson. “Owner Roy Yamaji was instrumental in being a mentor for starting our business, providing insight in how to be successful and sustain being successful.”
Equipment acquired from JMT includes two Takisawa TS-4000Y (booth #338536, part of Yamazen) turning machines, an AXILE G6 5-axis milling machine, an Axile G8-MT 5-axis mill/turn, and new TG-350 SAX from Taiwan Machine Tool. All are equipped with SCHUNK (booth #432010) workholding and SCHUNK's VERO-S quick-change pallet systems.
“Multi-Axis is in our name, so we do 5-axis milling and 6-axis turning to reduce part set-up time,” says Simpson. “Providing quick turnaround, often within a week, also requires using"> VERICUT (booth #133340) software to reassure ourselves that the first cut will be a good cut.” VERICUT is a leading industry software for simulating CNC machining to detect errors, potential collisions, or areas of inefficiency.
Simpson notes that both Axile machines feature controls from HEIDENHAIN (booth #339440), which was a happy accident.
“We needed a machine immediately. This was during the COVID period, and the only machine available had HEIDENHAIN controls, which are not well known on the West Coast,” recalls Simpson. He didn't really want the controller, but it arrived, and he grudgingly wrote all the post-processor scripts. He had to train himself because they couldn't bring people in during the pandemic.
“It turned out that the more I ran it, the more I thought it was awesome and wondered why somebody would buy anything else,” says Simpson. “I fell in love with HEIDENHAIN controls and decided they're going to be our focus as we build the business. We can train someone on them easily, and the control is accurate because it's a direct link between the encoders and the control, and it moves at lightning speed. We're trying to do everything as fast and as best we can, and we decided HEIDENHAIN was the better choice.”
Knowing a Guy
“Multi-Axis Technologies is the culmination of all the relationships we have built over the years,” says Simpson. “I say that in the truest form of relationships, such as with sharing knowledge. I didn't know machining until someone showed me, so that is a connection I have with somebody. Those connections run really deep.”
They also make for a much smaller community. While people break off from companies such as Blue Origin, Aerojet Rocketdyne, and Boeing, they remain connected like the fingers of a lighting bolt.
“In the manufacturing and engineering community, where does everybody meet? At IMTS,” says Simpson. “When you go there, you're like, ‘Oh, there's Steve from 3D printing. Oh, there's Craig, my old boss.' You reconnect with all these people that you haven't seen in a while that are on the same path, just wearing a different company shirt.”
“If you're looking to find ‘unobtainium,' your next tooling purchase, your next thing, IMTS is the place to go,” continues Simpson. “If the person you're talking to doesn't know the solution, he's got a guy that does. The community is so tight that somebody knows somebody, and I guarantee you'll find it at IMTS.”
Join your manufacturing community and see what doors open for you at IMTS 2024, Sept. 9-14, McCormick Place. Register now at IMTS.com/register.